Different types of chillers and how they work?
There are mainly two types of chillers Like Vapor Compression and vapor absorption chillers. Vapor Compression chillers use an electric compressor to force refrigerant around the system. According to the cooling of refrigerant, there are two types of Vapor compression chillers.
- Air Cooled
- Water Cooled
Depending on the compressor type, there are more different types of chillers. Like, Centrifugal chiller, Reciprocating chiller, Scroll chiller, Screw Chiller.
In this blog, we will explain the following types of chillers and why and when we should choose the perfect type of chiller.
- Vapor Compression Centrifugal Chiller (Water cooled)
- Vapor Compression Reciprocating Chiller (It can be Air cooled and Water cooled Both)
- Vapor Compression Scroll chiller Chiller (It can be Air cooled and Water cooled Both)
- Vapor Compression Screw Chiller Chiller (It can be Air cooled and Water cooled Both)
- Vapor Absorption water-cooled Chiller
- Hybrid Chiller
- Magnetic Bearing Chiller
- Heat Recovery Chiller (It can be Air cooled and Water cooled Both)
First I will explain the basics of Vapor Compression Air Cooled Chilled and Vapor Compression Water Cooled Chillers. After that we will discuss this in more detail. (Centrifugal chiller, Reciprocating chiller, Scroll chiller, Screw Chiller and Vapor Absorption Water Cooled Chiller)
Air Cooled Chiller:
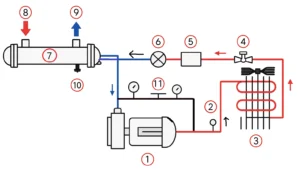
This is a proper picture of how an air-cooled chiller works. In the picture
- Compressor
- Pressure Gauge
- Condenser
- Shut off valve
- Filter dryer
- Expansion Valve
- Evaporator
- Water In (12°C)
- Water Out (6°C)
- Drain
- High/Low Pressure Protector (when the pressure in the compressor is too high it turn off the compressor)
- Condenser Fan
As you can see in the picture, Low-pressure refrigerant enters the compressor and it compresses the refrigerant gas. As a result, superheated high-pressure refrigerant gas move through the Pressure Gauge. For that reason, we can check the pressure of the refrigerant. If, due to any technical fault or any leakage issue happens. Then by watching the pressure gauge, we can notice these kinds of issues.
This Superheated high-pressure refrigerant gas moves to the Condenser. You can see there is a Fan, This fan cools the condenser and because of that heat exchange happens. During this heat exchange process, Refrigerant gas turns into a cold liquid form.
Then this High-pressure cold refrigerant moves to the Evaporator Through the shut-off valve, Filter dryer, and Expansion Valve.
Shut off valve: With this valve, we can stop the refrigerant flow in the system. This valve is important for maintenance work. If leakage issues happen, during parts changing and for any adjustment shut-off valve is required.
Filter dryer: It filters the liquid refrigerant and removes the moisture from it.
Expansion Valve: The Expansion valve expands the cold liquid refrigerant gas. Because of this, the pressure and temperature become much lower.
After passing the expansion valve, the cold refrigerant moves to the evaporator.
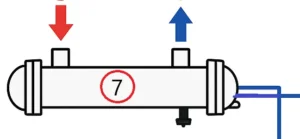
Under this thing, there is a heat exchanger coil, which is called an evaporator. See the picture below for more clarity.
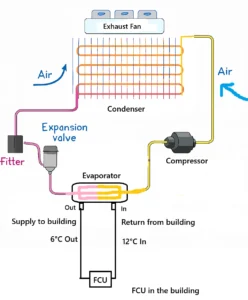
So the hot water from the building enters the evaporator. Here through the heat exchanger refrigerant absorbs the heat from the water and becomes low pressure gas. This low-pressure gas moves to the compressor again, and this is how this process runs continuously.
So, the hot water from the building cools down here. And this chilled water moves to the cooling coil of FCU/AHU. Where through the heat exchange, our place gets cold and the water gets hot (12°C)again, through the return pipeline this 12°C water moves to the evaporator, where it gets chilled (6°C) and moves to the FCU again. This is how this process works.
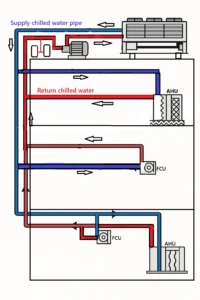
In the picture, the chilled water (6°C) from the chiller is moving to the FCU and AHU. After the heat exchange, the room gets cold and the water of the system becomes hot(12°C). Through the return pipeline this hot water (12°C) moves to the evaporator of the chiller. Then the evaporator makes it chilled (6°C) again. So, this process continues.
Advantages of a Vapor Compression Air Cooled Chiller:
– Costs less compared to the water-cooled chiller.
– Fast installation compared to the water-cooled chiller.
– Less maintenance
– It takes less space compared to the water-cooled chiller.
Disadvantages of a Vapor Compression Air Cooled Chiller:
– Short service life.
– Consume more electricity compared to the water-cooled chiller.
Water Cooled Chiller:
Air-cooled chillers and water-cooled chillers are almost the same. The only difference between them is that the air-cooled chiller Condenser is cooled by a high-speed fan and in the water-cooled chiller, the condenser is cooled by chilled water, which comes from the cooling tower. In the picture, you can see how chilled water is moving to the condenser to make it cool and after heat exchange the hot water returns to the cooling tower. Cooling towers make the water cool again and send it to the condenser. This is how this process constantly works.
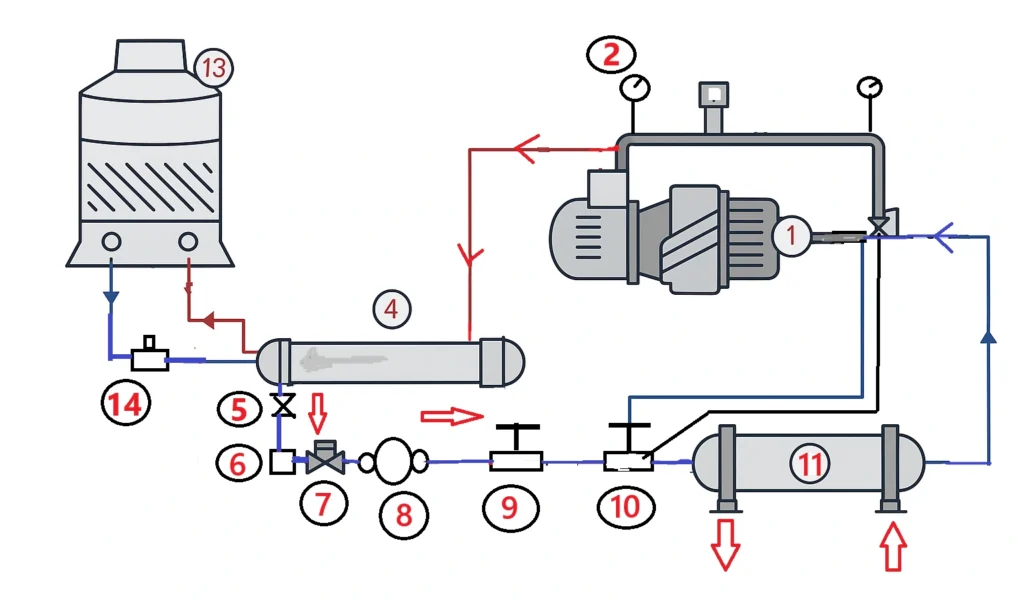
This is a proper picture of how an air-cooled chiller works. In the picture
- Compressor
- High-pressure gauge
- High/Low pressure protector (when the pressure in the compressor is too high it turn off the compressor)
- Condenser
- Shut off valve
- Filter dryer
- Shut off valve
- Liquid mirror
- Solenoid valve
- Expansion valve
- Evaporator
- Low-pressure gauge
- Cooling tower
- Pump
As you can see in the picture, Low-pressure refrigerant enters the compressor and it compresses the refrigerant gas. As a result, Superheated high-pressure refrigerant gas comes out through the Pressure Gauge and because of that, we can check the pressure of the refrigerant. If any technical fault or any leakage issue happens. Then, by watching the pressure gauge, we can identify these kinds of issues.
Through the high/low pressure gauge (When the pressure in the compressor is too high it turns off the compressor and when the pressure is too low it turns off the system to prevent frizzing and compressor failure issues.) this superheated, high-pressure refrigerant gas goes to the Condenser.
You can see in the picture that chilled water is coming to the condenser from the cooling tower. Here, heat exchange happens and because of condensation, refrigerant gas turns into a cold liquid form.
Then this High-pressure cold liquid refrigerant moves to the Evaporator Through the shut-off valve, Filter dryer, liquid mirror, Solenoid valve, and Expansion Valve.
Shut off valve: With this valve, we can stop the refrigerant flow in the system. This valve is important for maintenance work. If leakage issues happen, during parts changing and for any adjustment shut-off valve is required.
Filter dryer: It filters the liquid refrigerant and removes the moisture from it.
liquid mirror: it is a transparent glass on the system line for the visual inspection of refrigerant flow/moisture flow.
Solenoid valve: It is an electrically operated valve. It controls refrigerant flow to manage the cooling cycles and ensure energy efficiency.
Expansion Valve: The expansion valve expands the cold liquid refrigerant gas. Because of this, the pressure and temperature become much lower.
After passing the expansion valve, the cold liquid refrigerant moves to the evaporator.
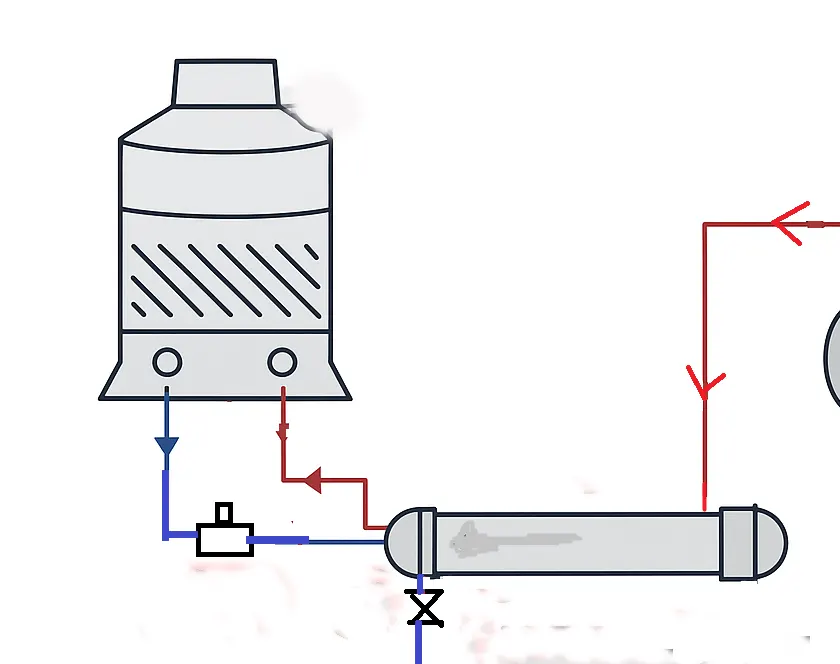
Under this thing, there is a heat exchanger coil, which is called an evaporator. See the picture below for more clarity.
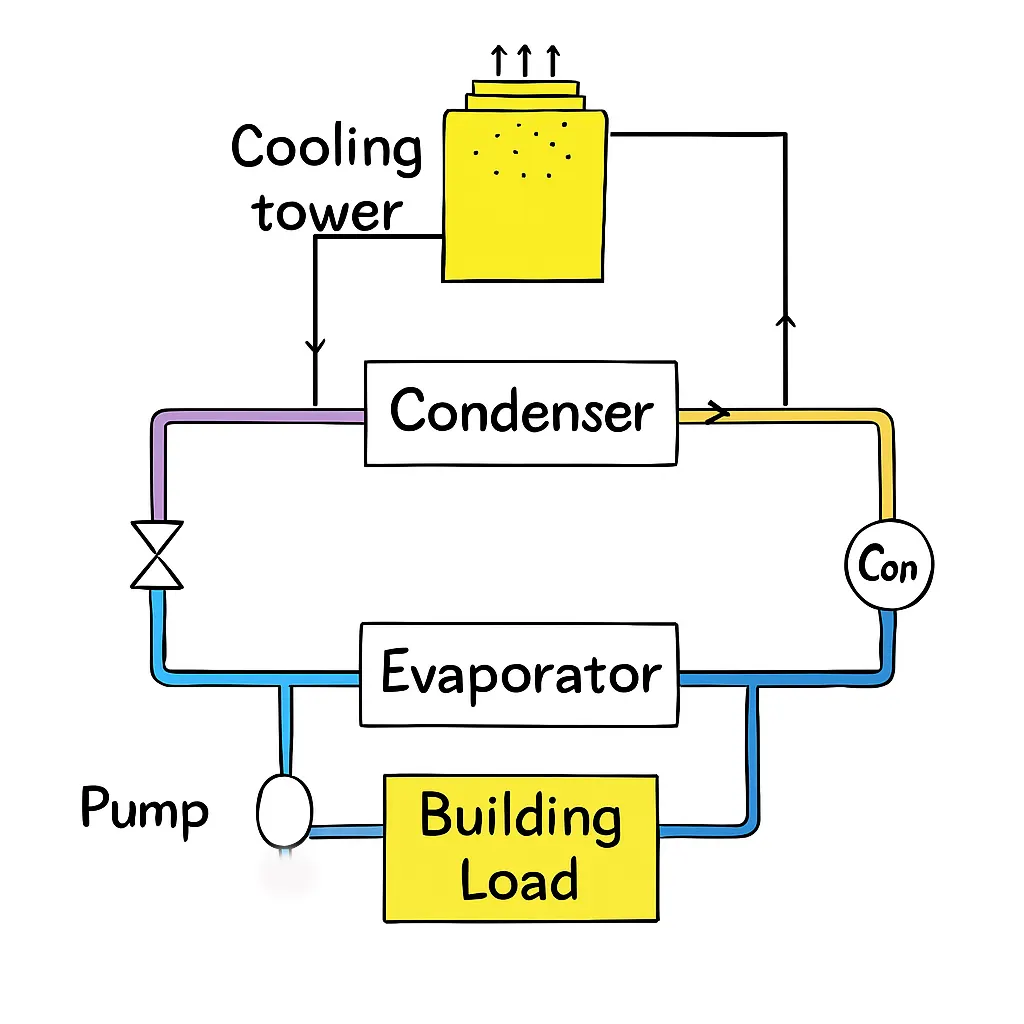
So the hot water from the building enters the evaporator. Here through the heat exchanger refrigerant absorbs the heat from the water and becomes low pressure gas. This low-pressure gas moves to the compressor again and this is how this process runs continuously.
So, the hot water from the building gets cooled down in the evaporator. And this chilled water (6°C) moves to the cooling coil of FCU/AHU (Building load). Where through the heat exchange, our place gets cold and the water gets hot (12°C)again, through the return pipeline this 12°C water moves to the evaporator, where it gets chilled (6°C) and moves to the FCU again. This is how this process works.
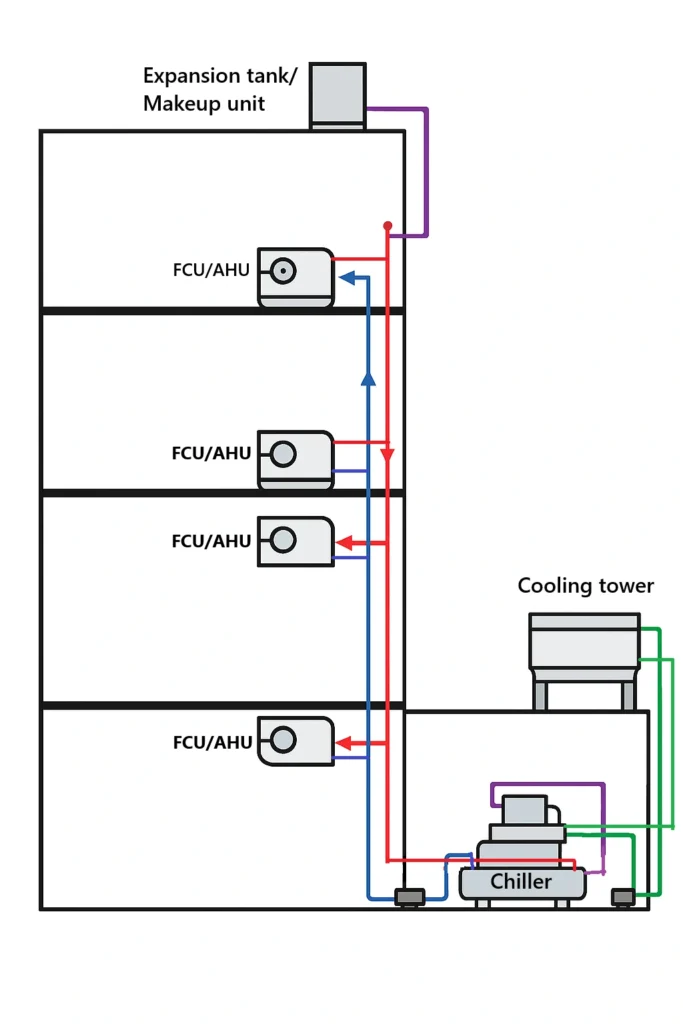
In the picture, the chilled water (6°C) from the chiller is moving to the FCU and AHU. After the heat exchange, the room gets cold and the water of the system becomes hot(12°C). Through the return pipeline, this hot water (12°C) moves to the evaporator of the chiller. Then the cold water from the cooling tower moves to the evaporator and the system water becomes chilled (6°C). This is how the evaporator constantly makes the system water chilled (6°C).
Advantages of water-cooled chiller:
– Less electricity consumption. (Highly energy efficient)
– Long service life
– High cooling capacity
Disadvantages of water-cooled chiller:
– High cost
– Require more installation time and maintenance cost compared to air cooled chillers.
– you need to use the basement or other building space for it.
– Required large space (Plant room) for Extra pump, water treatment, cooling tower and extra pipe.
1. Centrifugal chiller (water cooled):
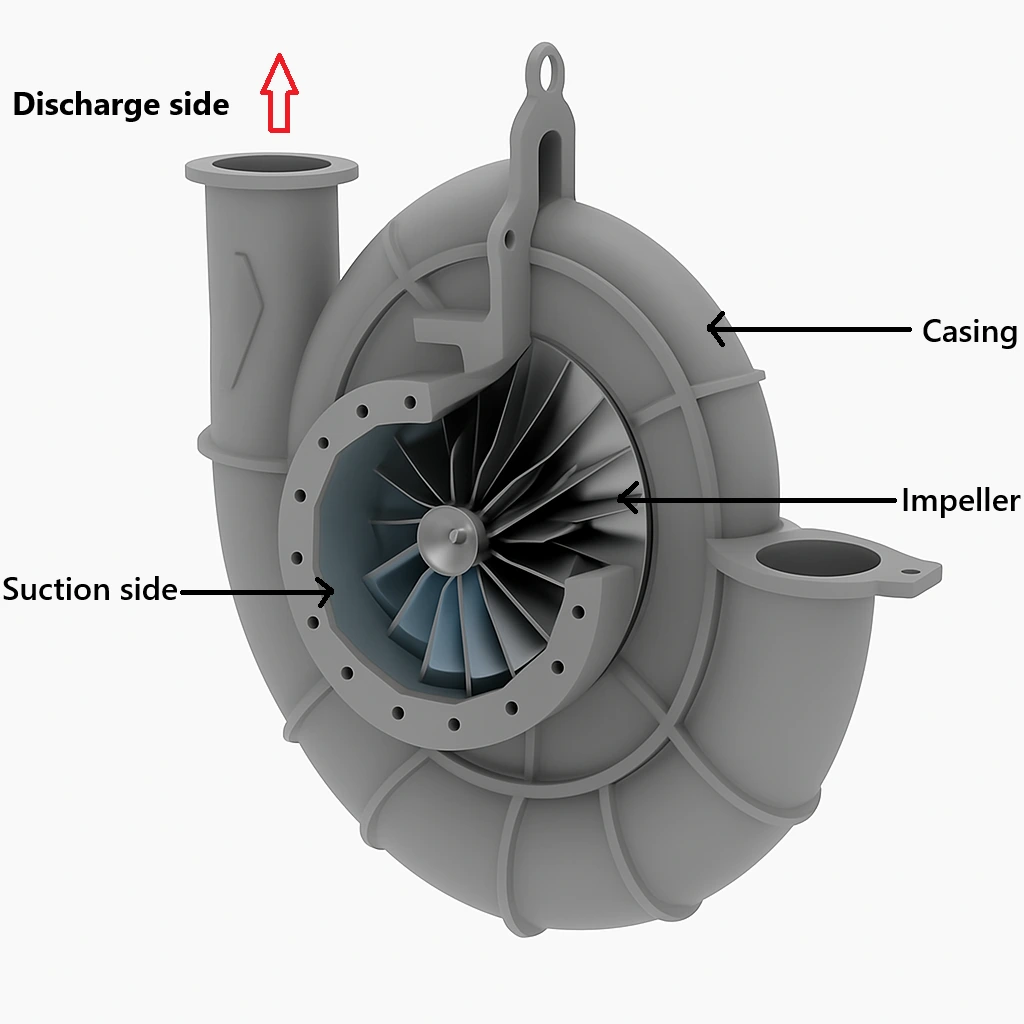
Centrifugal compressor is mostly used in water-cooled chillers because this compressor efficiently handles very large cooling capacities and require superior heat rejection capabilities of water-cooled condensers.
The impeller of this compressor rotates at very high speed, sucks in gas and accelerates it to such high velocities that in some cases the velocity of the moving gas reaches the speed of the sound. Before such high velocity gas is discharged, it is passed through a section of increased area. This causes the kinetic energy of the moving gas to get converted into static energy. This is how this compressor works.
In the below information you will find more information regarding centrifugal chiller:
- Water cooled chiller.
- used in medium-large cooling loads.
- You will find this chiller in 150-6,000 TR capacity.
- Use one compressor.
- Use one or two rotating impellers to compress the refrigeration and force it around the chiller.
- Capacity control through speed control and vane guides.
- COP (Coefficient of performance) of 5.8 to 7.1
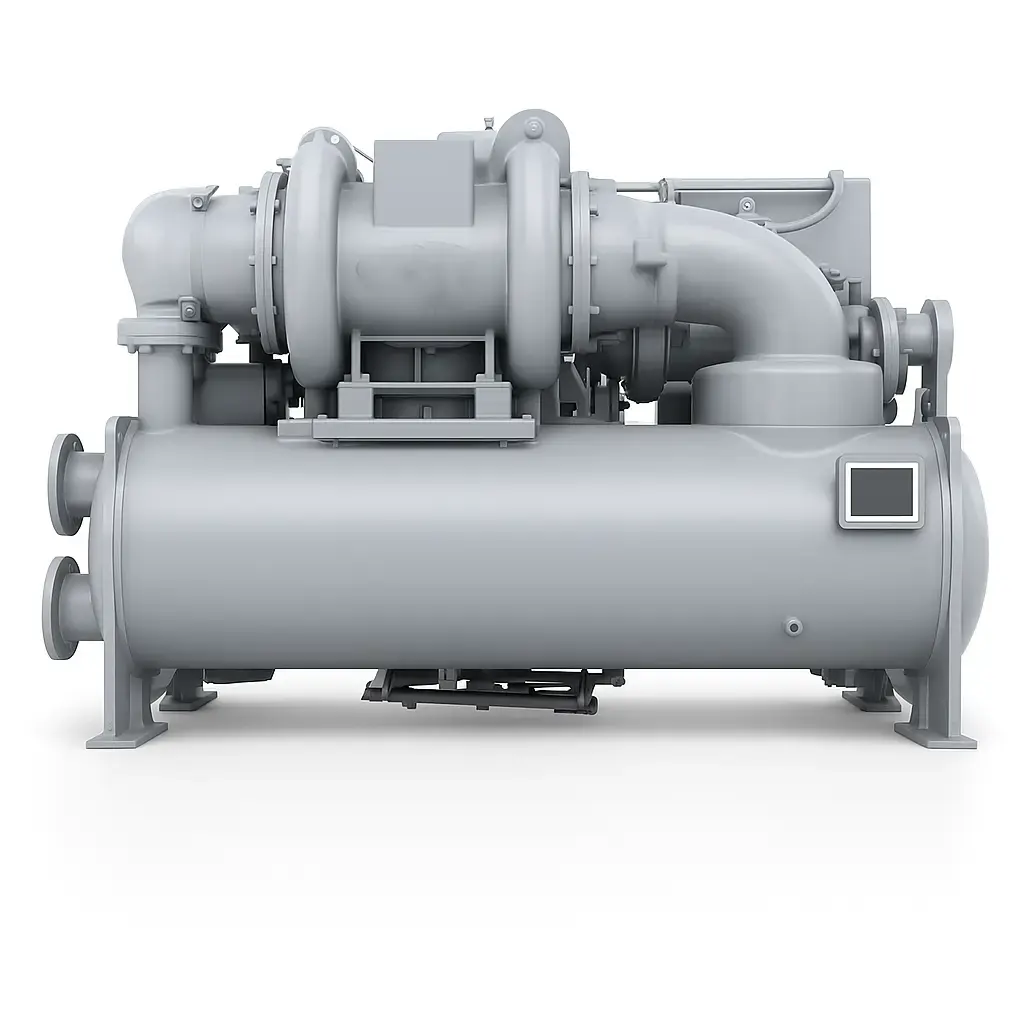
When to choose a Centrifugal chiller:
- When your system requires a high cooling load, like 200 TR – 1000 TR.
- When you have a reliable source of water. Because this type of chiller requires extra water compared to the air-cooled chiller. If you live in a place where water availability is an issue, then don’t choose this type of chiller.
- If you want to minimize the electricity bill then choose it. Centrifugal compressors consume less electricity while operating in full-load.
- When the cooling load requirement is very low the VFD can be utilized to maintain high efficiency.
- This kind of chiller requires more space. If you have enough space for cooling towers, condenser water pumps, water treatment systems then go for it.
- centrifugal compressors are sensitive to voltage fluctuations, so make sure you have a stable electricity supply.
Hare all processes are similar to the water-cooled chiller that I explained before.
2. Vapor Compression Reciprocating Chiller (It can be Air cooled and Water cooled Both):
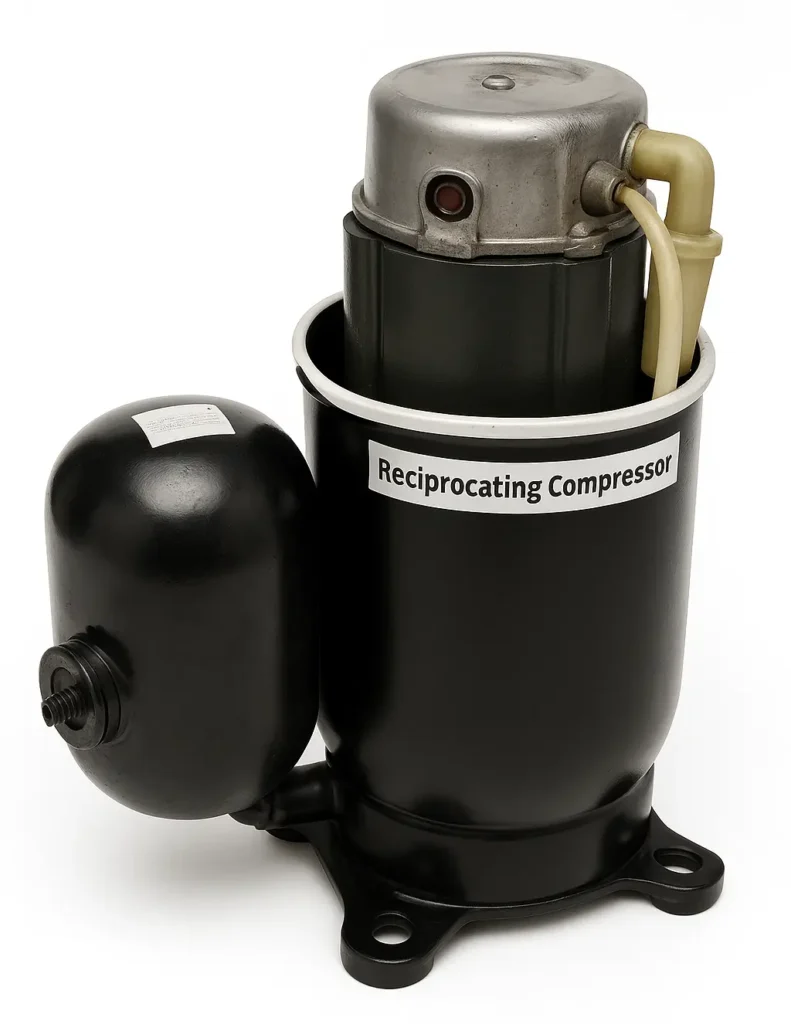
This is an old technology. Reciprocating compressors can be used in Air cooled and Water cooled both types of chillers. It is used for those places where the cooling load requirement is small to medium. If we talk about the availability, then you will find 50 Ton – 500 Ton capacity of reciprocating chillers.
Reciprocating compressors use a piston and chamber to compress the refrigerant gas. The COP of it is 4.2 – 5.5
This compressor contains an assembly of a piston and a crankshaft. The purpose of the assembly is that when the gas is sucked inside the compressor the crankshaft mechanism will produce a reciprocating motion and will move the piston to compress the gas Based on how the cylinder inside the compressor motor reacts with the working fluid.
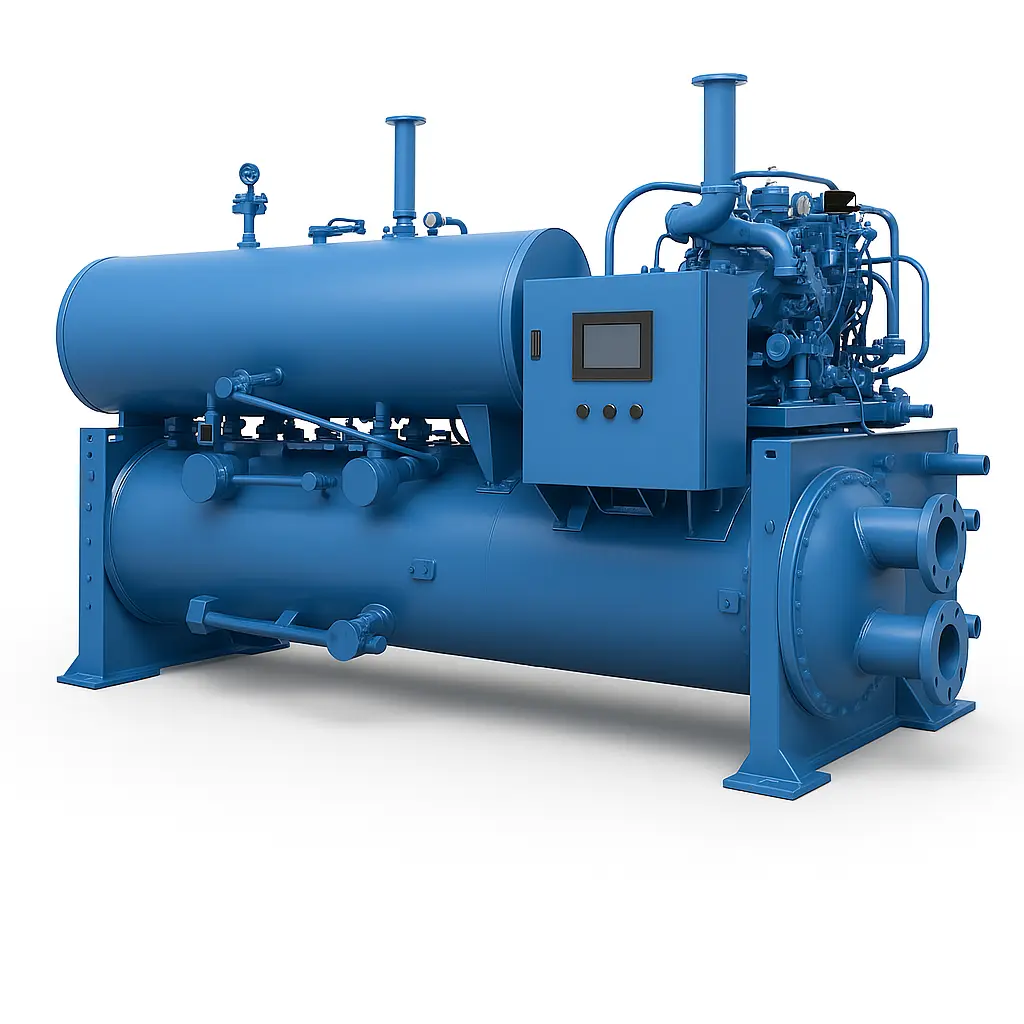
When to choose a Reciprocating chiller:
- When your required cooling load is low to medium (below 200 tons/700 kW), In this condition centrifugal or screw chillers become less efficient. So, in this case old is gold.
- When the installation budget is low.
- If you have space issues then you can go for the reciprocation air cooled chiller.
- Well as it is an old technology, if HVAC technicians are unavailable to repair, reciprocating compressors will be widely understood by car engines because of the semmler technology.
- If water availability is an issue in your area, then go for the Reciprocating air cooled option.
- Where the cooling load is highly variable (Load up & down), reciprocating compressors handle this better than screws or centrifugals without efficiency penalties or wear issues.
- If one compressor gets damaged it only impacts a fraction of total capacity, because if one compressor fails, the others keep running unlike a single large screw/centrifugal.
3. Scroll Compressor Chiller (It can be air-cooled and water-cooled Both):
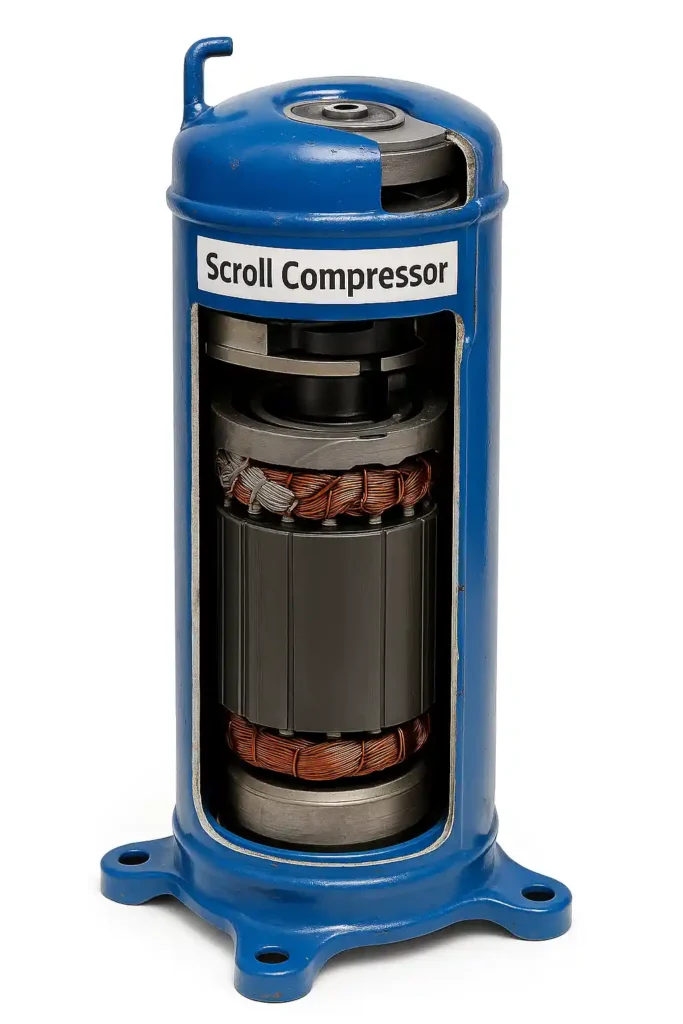
It is one of the quietest compressors in operation. Scroll compressors can be used in Air cooled and Water cooled both types of chiller. It is used for those places where the cooling load requirement is small to medium. 40 Ton – 400 Ton Capacity of scroll chiller is available.
Scroll compressors use two spiral plates to compress the refrigerant-(One fixed in place/ one rotates). COP for Air cooled Scroll Compressor Chiller is 3.2 – 4.86 and the COP for Scroll Compressor water cooled chiller is 4.45 – 6.2
The rotating mechanisms in the scroll compressor are a pair of interleaved spiral-like vanes.
Often one of the scrolls is fixed and the other scroll operates eccentrically. This movement draws in and compresses gases. The very small clearance between the fixed scrolls leads to high volumetric efficiency.

When to choose a Scroll chiller:
- Ideal for those places where the cooling load is around 200 tons
- If your budget is low, then you should go for a scroll chiller, because the cost of scroll chiller is lower compared to other chillers. (it also depends on which brand you purchase)
- Compared to other chillers, scroll chillers are compact. So, if space is an issue for your project, then go for it.
- Minimal vibration, easy to maintain and less noisy.
4. Screw Compressor Chiller
(It can be air-cooled and water-cooled Both):
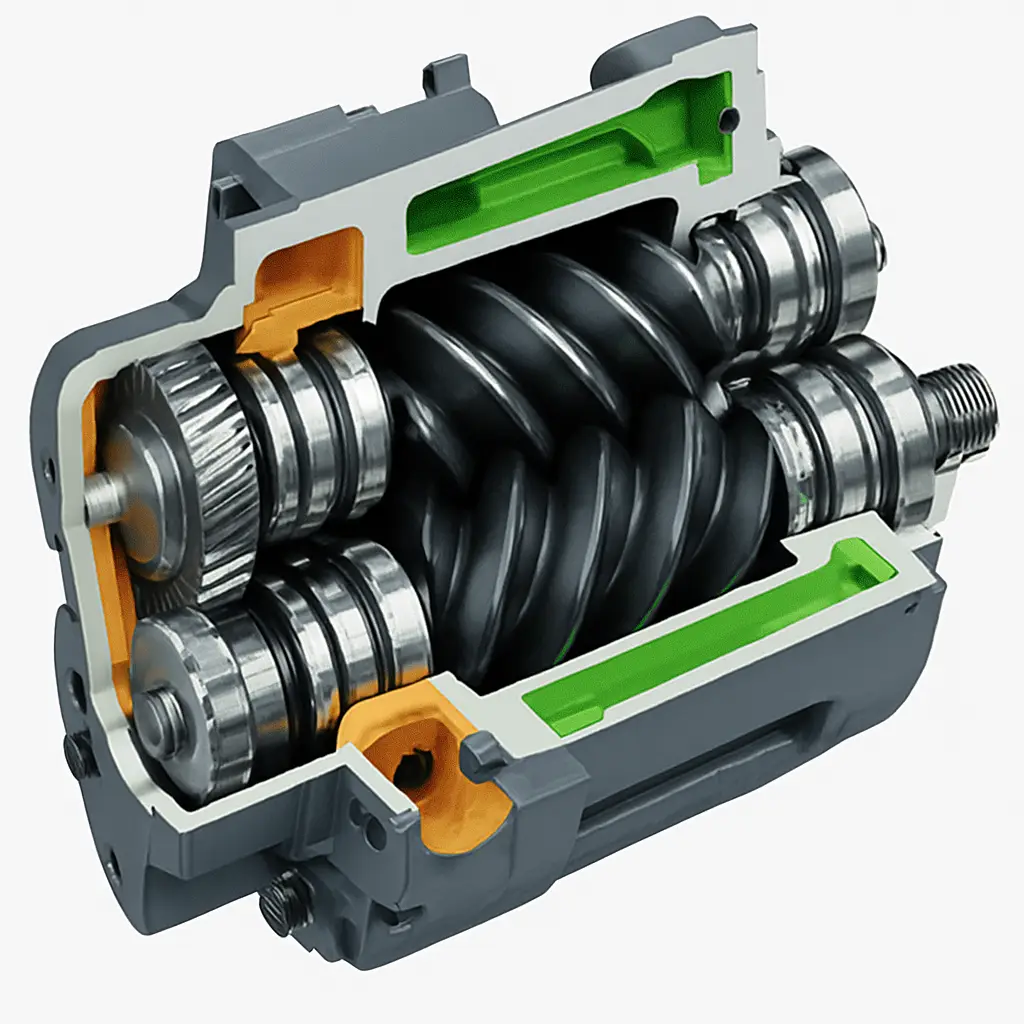
Screw compressors can be used in air cooled and water cooled both types of chiller. Mostly used in places where the required cooling load is small to medium. A screw chiller is available under 70 to 600 tons of capacity. In a water cooled chiller there will be one screw compressor and in a water cooled chiller there will be two screw compressors. The capacity is controlled via speed control or slider.
- COP for Air cooled chiller = 2.9 – 4.15
- COP for water-cooled chiller = 4.7 – 6.07
Screw compressors contain a pair of helical screws, referred to as a male screw and a female screw. The rotating motions of the screws are responsible for drawing in gases from the input of the compressor. The gas is drawn in a continuous sweeping motion. The gas is drawn in a continuous sweeping motion. They don’t make much noise when they operate, and the compressor does not vibrate significantly during runtime.
When to choose a Screw chiller:
- If because of any technical fault, refrigerant moves to the compressor, Screw compressors can handle small amounts of liquid slugging better than centrifugal without catastrophic damage.
- Screw compressors deliver very high torque at low RPM, for that reason start-up stalling issues don’t happen in screw chillers which is common in Centrifugal.
- Screw compressors produce lower-frequency noise, compared to centrifugal compressors.
Choose screw chillers not just for “medium capacity,” but when operational resilience, mechanical forgiveness, power quality tolerance, or extreme environmental adaptability outweigh the pursuit of peak theoretical efficiency. Their ruggedness shines where centrifugal are too sensitive or complex to maintain reliably.
5. Absorption chiller (No Compressor):
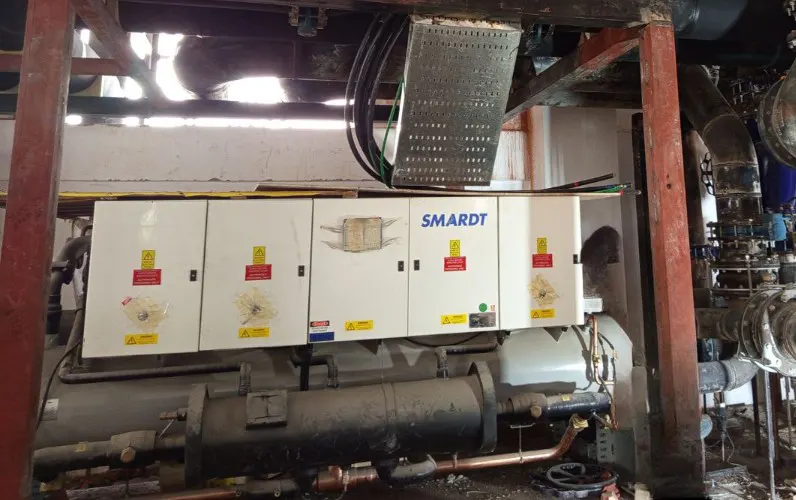
Absorption chillers use heat to drive the refrigerant process. In industrial projects if there is a source of hot water or steam then the absorption chiller is perfect for that place. This type of chiller is also used in hospital, swimming centers. There is no compressor in this type of chiller. If we talk about the availability, then you will get a 70 to 1400 tons capacity absorption chiller.
COP of Vapor absorption chiller is 0.6 to 1.9
When to choose a Vapor absorption chiller:
- Choose Vapor absorption chillers if your place has any additional heat source. Normal chillers run with only electricity but vapor absorption chillers operate with external waste heat. Because of this it will save a lot of electricity consumption cost for your place.
- This kind of chiller does not need any compressor to operate. For that reason you will face less noise and vibration issues.
- In a place where you don’t have any additional waste heat, don’t choose an absorption chiller. Because in that condition you will need a generator or electricity to make hot water which is inefficient. On the other hand in any place like industrial space, Hospital or swimming center have westage heat source, then among all types of chiller that exist vapor absorption chiller will provide you better efficiency.
How Vapor Absorption Chiller Works/ Working Principle Of Vapor Absorption Chiller:
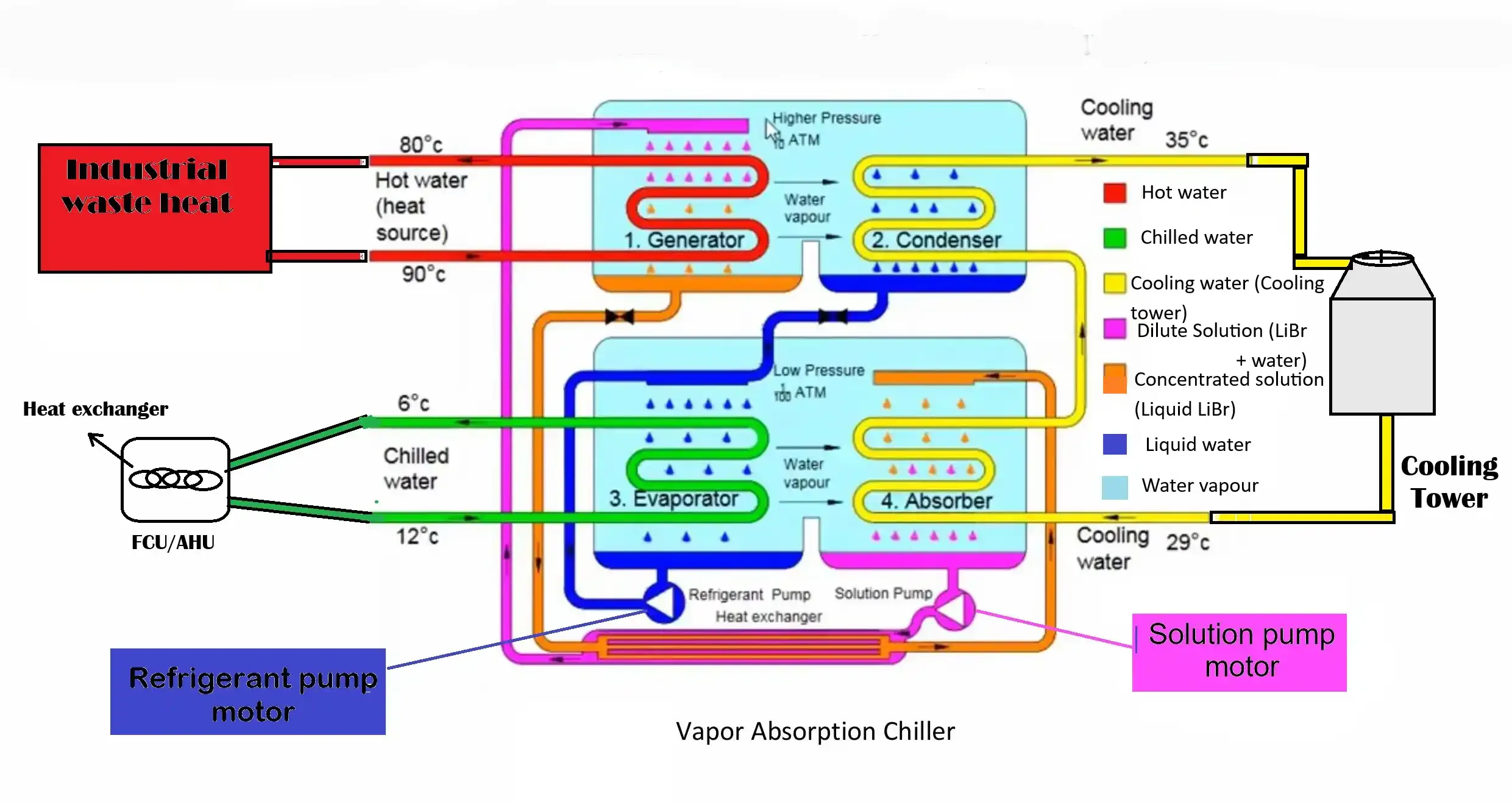
Regular refrigerant has not been used in absorption chillers. Instant of refrigerant gas, Lithium bromide and water solution used in this chiller. As you can see there are two sections. 1) High pressure section & 2) low pressure section.
During the heat exchange process this water and liquid Lithium Bromide move high pressure to low pressure section and this is how vapor absorption chillers work.
If you want to learn more about the working principle of vapor absorption chillers then read this blog, here i explained everything in the easiest way with proper pictures.
Working Principle of Vapor Absorption Chiller
6. Hybrid Chiller:
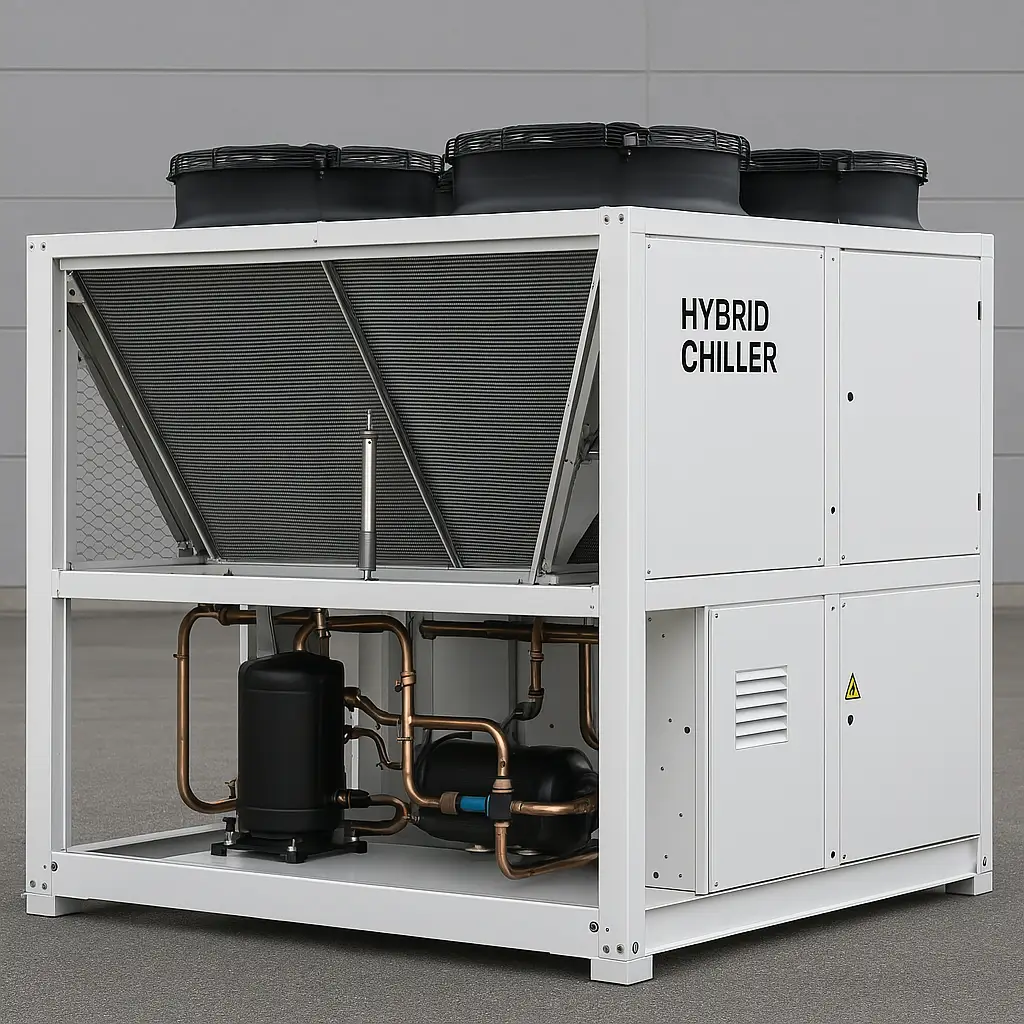
1. Till now, we have talked about chillers which are air-cooled or water-cooled. But there are chillers that use two methods to cool, like hybrid chillers. Hybrid chillers cool two ways like an air-cooler & also use water evaporation. There are two compressors in a hybrid chiller. So if one stops working, the chiller runs with the 2nd compressor.
2. Because hybrid chillers cool the refrigerant by water evaporation, they run more efficiently compared to other chillers.
COP of the Hybrid chiller is 5
3. Hybrid chillers are perfect for places where the cooling load changes constantly, such as in offices, hospitals, or data centers.
50 to 200-ton capacity Hybrid chiller is available. This kind of chiller is good for places where the cooling load requirement is low to medium. They are built as one compact unit.
4. This type of chiller doesn’t need a cooling tower. So it takes less space & time to install.
5. It costs less compared to the water-cooled chiller and costs more compared to the air-cooled chillers. But in the long term, a hybrid chiller will save a lot on electricity bills because of its efficiency.
7. Magnetic Bearing Chiller:
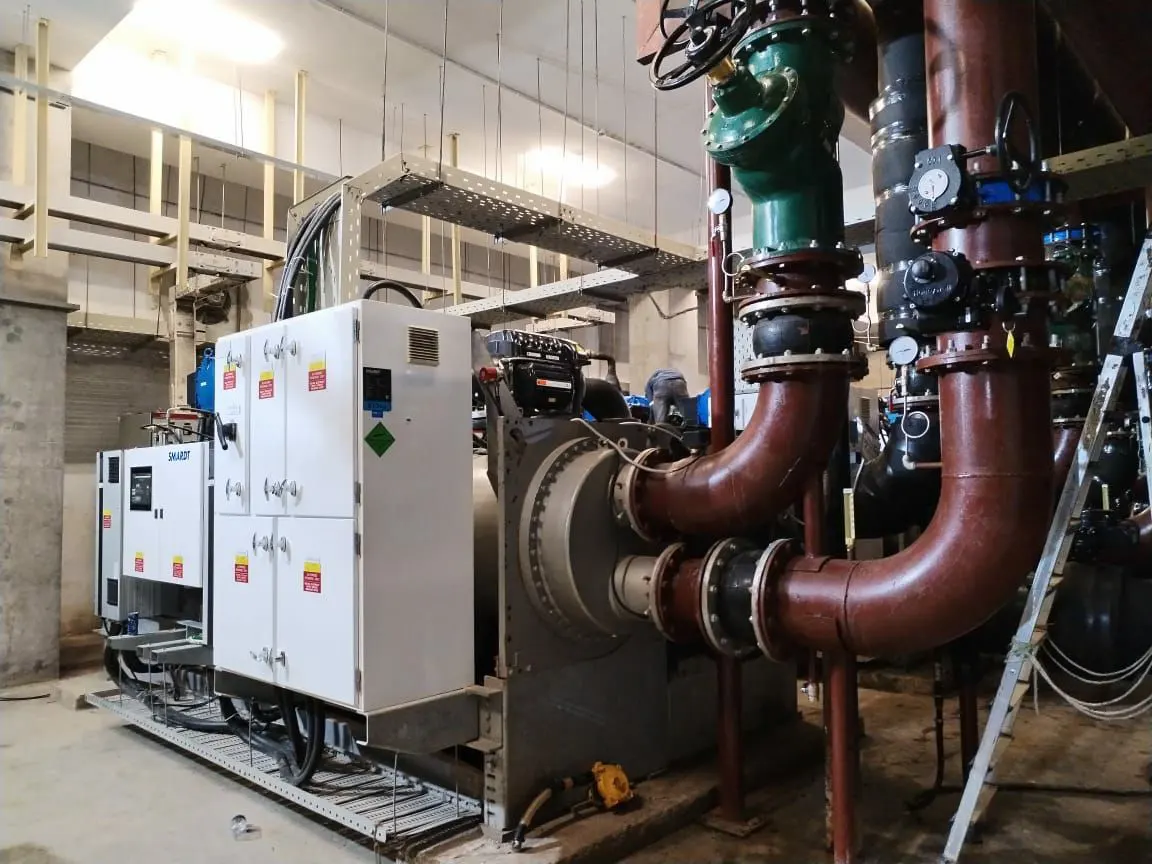
1. Magnetic chillers hold the moving parts by using magnets and because of that, oil isn’t needed for it. Also, the parts didn’t contact each other; for that reason, the Magnetic Bearing Chiller is very quiet and they can adjust their speed quickly as per the cooling load requirement.
2. In Magnetic Bearing Chillers, the parts don’t contact each other; for that reason, energy is not lost because of friction-related heat, which makes it efficient.
3. It’s great for those places where energy efficiency is the first priority and where the cooling load requirement is medium to high. The available capacity for this chiller is 60 to 1600 tons.
4. Although the Magnetic Bearing Chiller comes with a compact design, it still takes more space compared to the air-cooled or hybrid chiller.
5. It costs more than all the chillers. Although the initial cost is very high, in the long term you will be happy because of efficiency & low maintenance cost.
6. Magnetic Bearing Chillers took a similar time to install, like water-cooled chillers do.
Advantages of Magnetic Bearing Chiller:
1. Consume less electricity
2. It makes less noise.
3. Has no oil parts and causes low maintenance costs.
Disadvantages of Magnetic Bearing Chiller:
1. The initial cost is very high.
2. Need specialized trained technicians for maintenance work because it is uncommon compared to the other chillers.
8. Heat Recovery Chiller:
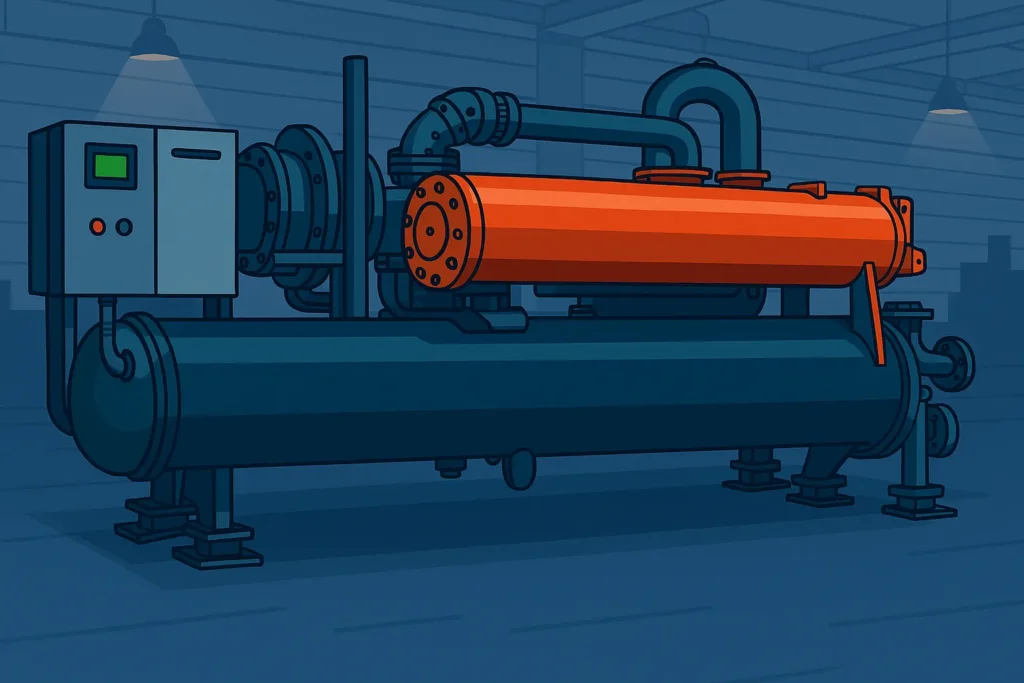
1. This type of chiller provides chilled water for cooling and also provides hot water for different uses. Instead of wasting the heat of the condenser, Heat Recovery Chillers use it to generate hot water at around 60°C. Heat Recovery is a system, you can install on any air-cooled or water-cooled chiller. To do this, you need to modify the condenser area. This modification will take a little more space but this will definitely be worth it.
2. Compared to screw, centrifugal, scroll and reciprocating chiller this is more efficient. On the other hand, you are getting a hot water source at a cheap price.
3. Heat Recovery chiller used for hotels, hospitals, offices and factories.
4. Higher price than normal chillers because of additional work in the condenser area.
But in the long term, you don’t need to have an additional unit for the hot water system & you get better efficiency.
5. It takes more time to install, because you need to work with additional pipes and valves, so that the hot water can move properly. Although it takes more space, it also saves space because you don’t need to have a separate hot water generator.
Advantages of Heat Recovery Chiller:
- Efficient because it reuses heat.
- More eco-friendly compared to others.
- Quiet compared to air-cooled chillers.
Disadvantages of Heat Recovery Chiller:
- Chiller unit price is high.
- Require extra space for installation.